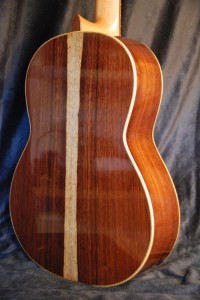
There are many different instrument finishes available, each of which has both good and bad features. Factory guitars with UV cured polyurethane finishes are almost completely indestructible, but leave the instrument with a thick coat of finish that dampens the sound. Nitrocellulose lacquer is quite protective, but it has a tendency to craze over the years and requires the finisher to use an explosion proof spray booth (or greatly annoy the neighbors with horrid fumes by spraying outside). There is a new class of water-based lacquers that can be sprayed to provide protection, but they leave the color with bluish tints and the result always looks plastic.
All of these inventions are designed to speed up the finishing process, and have resulting drawbacks in tone or color. I prefer to use the ancient and still very functional shellac as the finish on my instruments. When applied via the French Polish process, the result is a depth of clarity that cannot be seen with other finishes, while maintaining a very thin finish that does not interfere with the tone of the instrument.
French polish is applied in a very labor intensive process via hundreds of microscopically thin coats. A pad that is damp with finish is rubbed across the instrument to deposit shellac in extremely thin coats that dry almost instantly. The resulting finish holds up to daily use with cleanup requiring only a soft dry cloth. It is by no means as indestructible as a thick factory UV cured polyurethane finish, so care should be used in keeping the instrument in good health. One key advantage to shellac is that it is extremely repairable. It can be touched up if it gets dirty or if there is wear in the finish over time.
For an example of how much damage can be restored in a French Polish, check out this video of a badly damaged cedar top I restored:
If you are local to San Diego, feel free to drop off any guitar you purchase from me for an inexpensive touch up on the finish if it starts needing a bit of attention.